Engineering Student Makes Respiration Masks in His Garage for Local Health Care Workers
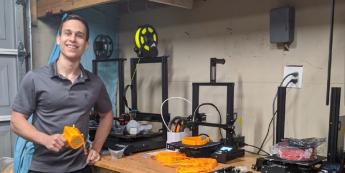
Working with medical professionals, a Cal Poly engineering student has helped design and create 60 respiration masks in his garage using 3D printers, and he plans to create even more to help address the nationwide shortage of the crucial medical protective gear.
Cristian Sion, a double major in materials engineering and manufacturing engineering, was contacted by Jeremy Ralston, a facilities engineer at the San Luis Obispo Surgery Center, who asked if he could help create a N95 mask, which can block at least 95 percent of very small (0.3 micron) particles.
“I jumped at the opportunity and made a few prototypes for him the same day,” Sion said.
N95 respirators and surgical masks are examples of personal protective equipment (PPE) that are used to protect the wearer from airborne particles and from liquid contaminating the face, according to the U.S. Food & Drug Administration. Ralston said he was concerned about a shortage of N95 masks for healthcare workers and first responders.
Working with Dr. Clint Slaughter, an emergency room physician at both French Hospital Medical Center and Arroyo Grande Community Hospital, the trio also found that other 3D-printed mask designs needed improvements.
“During testing, several doctors and nurses noted that it was difficult to breathe using the original design,” said Sion of a popular Billings Respirator design that was the brainchild of a Montana neurosurgeon. “I helped increase the filter size by 50 percent.”
Ralston initially reached out to Cal Poly’s amateur radio club for someone with a 3D printer and was referred to Sion. The engineering senior from Los Angeles purchased his first 3D-printer kit for $180 about two and a half years ago as part of a class research project and has since added more.
“3D printing started off as a hobby for me,” he said. “I used to think it was silly at first but soon learned you can make incredible things with it.”
A 3D printer can create solid three-dimensional objects from a digital file. Sion eventually started a 3D-printing service, Additive Engineering, because he wanted to learn about business and live by Cal Poly’s Learn by Doing ethos. He created dozens of parts for fellow students and performed design and printing for several customers.
When the global COVID-19 pandemic broke, he was already thinking of what he could do when Ralston reached out to him. Medical providers are especially vulnerable to contracting the virus, which has resulted in more than 16,000 deaths nationwide.
While homemade masks are gaining popularity, they are not approved N95 products by FDA or National Institute for Occupational Safety and Health (NIOSH).
Sion, Ralston and Slaughter continue to work on the masks as they await approval.
“We all have the same mindset of helping the community,” Ralston said.
The masks could be used by the general public first, Ralston said, with production likely to increase by two to four times once shortages progress in healthcare settings.
While French Hospital and Arroyo Grande Community Hospital currently have what is described as “adequate” PPE reserves for the next couple of months, Slaughter said, an increase in patients could quickly change that status.
“This is the reason that I’ve been working with Cristian and Jeremy, as well as hospital administration, to have locally producible means to extend our PPE supply,” he said.
The group has created a website, www.slorespirator.org.